Conveyor Services
Live Automation Group provides electrical and mechanical services for conveyor systems, including installation, maintenance, and system optimization. Projects range from small transfer sections to complex, large-scale material handling systems. Services are designed to maintain operational efficiency and system reliability over time.
Installation Services
Conveyor Installations – Installation of new conveyor systems for applications such as manufacturing, packaging, and logistics.
Custom Configurations – Conveyor layouts and mounting solutions based on facility layout, material flow, and system requirements.
Integrated Field Support – Field technicians trained in both mechanical and electrical installation for cohesive system integration.
Maintenance Programs
Preventive Maintenance – Scheduled inspections, cleaning, lubrication, and tensioning to maintain system health and identify potential issues early.
On-Site Support – Field maintenance services for addressing mechanical failures and supporting routine service needs.
Beneifits of a Maintenance Plan
Extended Equipment Lifespan – Reduces wear and increases system longevity.
Minimized Downtime – Early issue detection reduces the likelihood of unplanned outages.
Cost Efficiency – Limits the need for emergency repairs and replacements.
Workplace Safety – Supports proper function of safety components such as E-stops and guards.
Energy Performance – Maintains optimal operating conditions for energy savings.
Product Consistency – Reduces material handling disruptions that can affect product quality.
Regulatory Compliance – Helps maintain OSHA and industry-specific standards.
System Optimization – Supports efficient throughput and equipment performance.
Maintenance Tasks Include
Belt Maintenance – Belt inspections, cleaning, tension adjustments, and alignment verification.
Component Maintenance – Inspection and servicing of mechanical components such as rollers, chains, motors, and bearings.
Safety Checks – Testing of safety systems, including emergency stops, grounding, and sensors.
Maintenance Planning – Use of CMMS (Computerized Maintenance Management System) for scheduling, record-keeping, and tracking labor, parts, and costs.
Certifications & Trainings
LAG’s team has completed the OSHA 30 and OSHA 10 course to promote safe and healthful work environments
LAG’s Team also have MSHA certificate, allowing us to effectively service customers where required. This certification highlights our commitment to industry standards and safety.
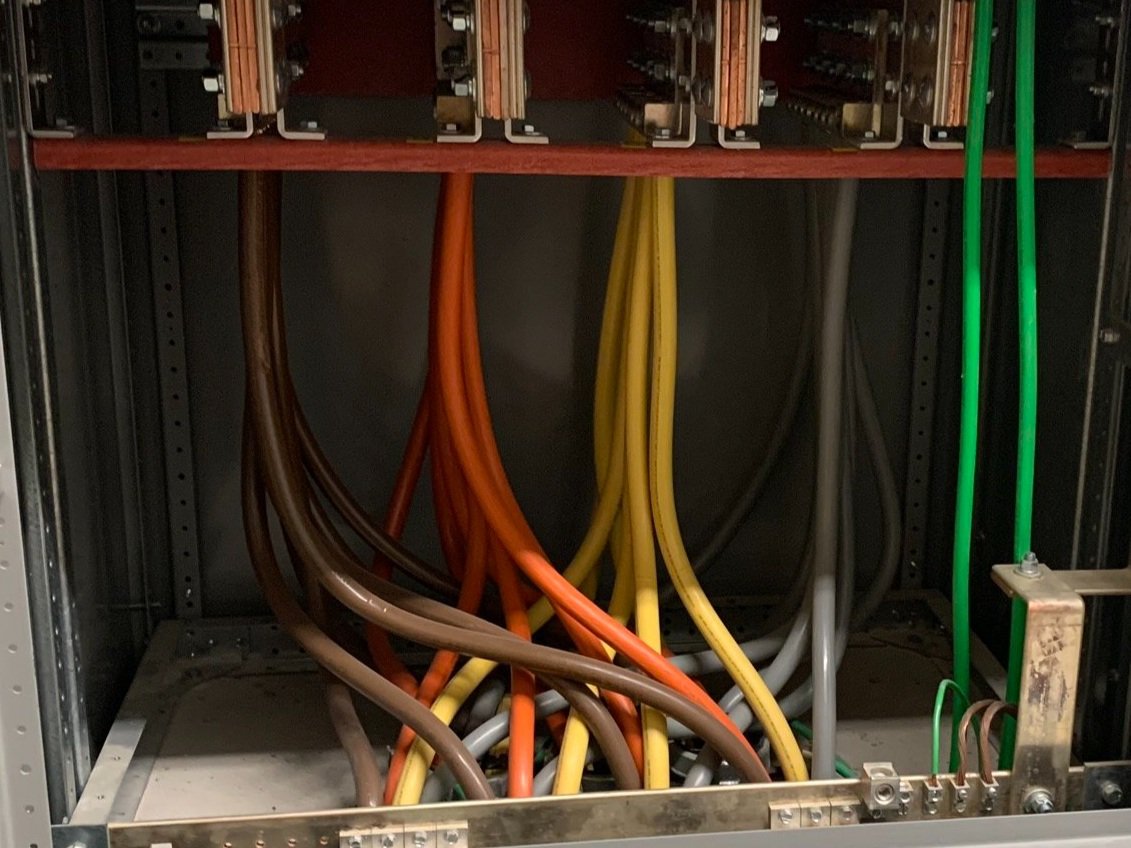